Engineers and rocket scientists love data. So no surprise the NASA thrust oscillation mitigation team has been gathering reams of data to best understand how to design an integrated vehicle that avoids thrust oscillation. This week at Ames Research Center, Moffett Field, Calif. NASA and industry engineers reviewed the latest progress to qualify and validate our understanding of thrust oscillation problems and solutions.
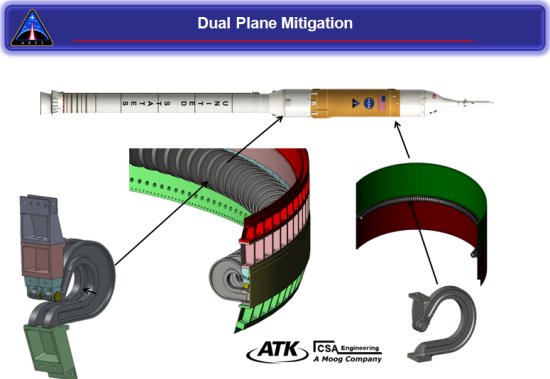
For those new to this issue, thrust oscillation is a phenomenon that can appear in all solid rockets where pressure created during launch conditions creates an up-and-down vibration at a frequency that could impact crew situational awareness or health. For Ares I, engineers expect a smooth ride up from liftoff to 115 seconds, but as the first stage nears burnout, thrust oscillations could pose a problem for a few seconds impairing the crew’s ability to read displays and respond to what they see.
Since the previous technical interchange meeting (https://blogs.nasa.gov/cm/blog/Constellation.blog/posts/post_1239311627391.html) several things have changed. Orion and Ares designs have matured and very helpful measurements have been captured during liftoff of the STS-126, STS-119 and STS-125 space shuttle missions which validate assumptions about how the solid rocket pressure oscillations occur in-flight. Mathematical modelers have an improved understanding of vehicle responses to candidate hardware designs. And finally, with the conclusion of the crew situational awareness testing, a new requirement has been proposed based on that work.
Constellation engineers have been pouring over new data to pinpoint several important factors that will drive optimal thrust oscillation fixes.
First, two important numbers to keep in mind: 12.3 Hz and .7g.
The thrust oscillation frequency of Ares I five-segment solid rocket motor is predicted to be approx. 12.3 Hz. By comparison, the shuttle’s four-segment solid rocket motor thrust oscillation frequency is 15 Hz. Ares I is a bit lower because it is longer. Think of an organ pipe: the longer the pipe, the lower the natural frequency. The goal of any mitigation is to minimize the effects on the crew due to the first stage thrust oscillation. There are two basic ways to do this: “de-tune” the vehicle stack or increase damping in the system. “De-tuning” is another way to say frequency separation — moving the natural frequencies of the Ares I vehicle and the Orion spacecraft away from 12.3 hz. Damping absorbs the extra energy in the system and can be targeted to specific frequencies. The goal of any mitigation system, or combination of systems, is to de-tune the vehicle approximately 1.5-2 Hz away from the vehicle’s natural resonance and avoid any problematic thrust oscillations with 99% certainty.
Since the Gemini era, NASA spacecraft designers used a limit of .25g peak as a safe threshold against these problematic longitudinal pressure oscillations. Based on increased fidelity gained through the crew situational awareness test series, the Constellation Program expects to set a new threshold, limiting the maximum peak to .7g, with a mean vibration level to not exceed .21g’s rms (root mean square) for any five second period during first stage flight.
Keeping these figures in mind, the team scrutinized proposed hardware solutions and how well each system, or combination of systems, will impact the integrated vehicle. Each thrust oscillation simulation includes over 10,000 analysis points including variations in forcing function, structural frequency response, and mode shape to provide an accurate assessment of how mitigation solutions will actually work in flight.
Design solutions under active development include passive single and multi-plane C-spring isolators, and mass absorbers called a Tuned Oscillation Array (or TOA). Work also continues on a LOX damper, which uses the slave mass of the Upper Stage liquid oxygen propellant to dampen out vibrations. Subscale hardware for two LOX damper designs — a bellows and diaphragm — have also been built and tested in the lab. All candidate solutions are being worked full force, and full steam ahead, to meet these updated parameters.
Initially, a dual plane C-spring isolator system was too heavy to incorporate into the overall vehicle design. The updated designs use titanium, not steel for the isolator springs, improving overall system performance while reducing the weight of the system. The weight reduction made a dual-plane C-spring isolator system much more attractive as a design solution and it is out-performing the other passive systems. The next step is to make a decision about how best to implement a dual plane solution into integrated designs. Nothing is off the table yet, as the team continues to refine which fix is most robust.
The team’s analysis during this session reemphasized that thrust oscillation is not just a first stage or Ares problem. It’s a technical challenge that impacts the entire vehicle and can be solved by an integrated team of Ares and Orion engineers. Because of this, final decisions about which solution is optimal will be incorporated as an issue into the Constellation Preliminary Design Review scheduled for late this year. The team also looks forward to capturing data from the upcoming five segment development motor test (DM-1) and Ares I-X flight which will further characterize how the in-line vehicle responds.
Reported by Jennifer Morcone, NASA MSFC public affairs