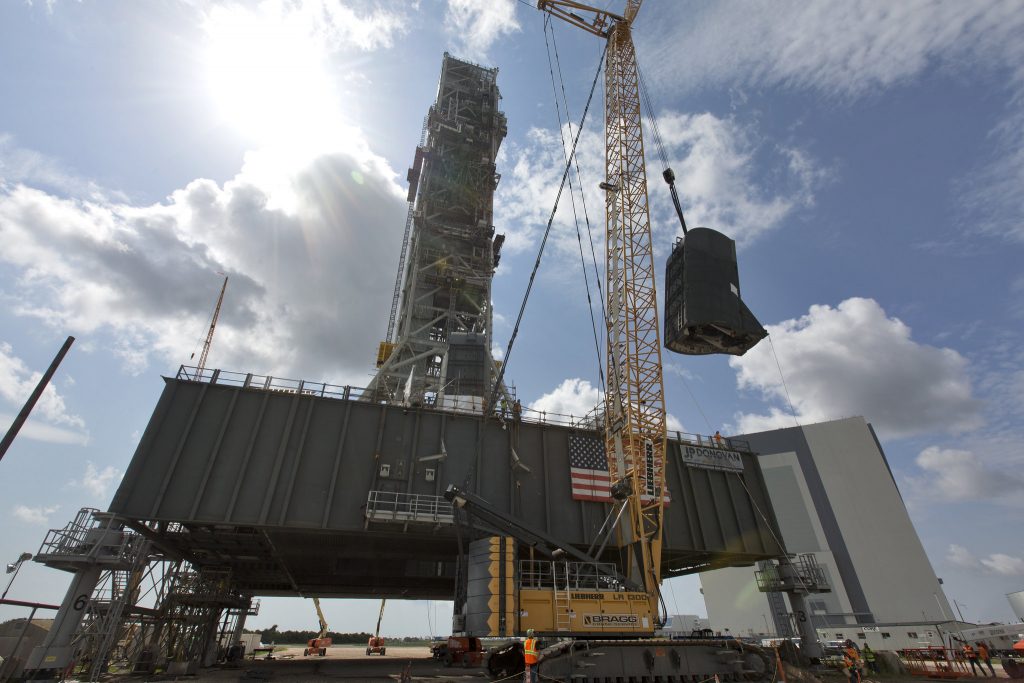
Operating a heavy-lift crane and working with some of the strongest metals on Earth takes precise diligence, skill and patience. Bragg Crane & Rigging Co. of Long Beach, California, has worked in the industry since 1946, and its team members embody these skills each day as they lift and weld a launch structure that will take America back to the Moon and on to Mars.
For the past four years, Bragg Crane & Rigging Co. has been supporting Kennedy Space Center’s Exploration Ground Systems (EGS) program, playing a crucial role in preparing the program’s mobile launcher for NASA’s Artemis missions. The company has had unique opportunities to lift and install most of the critical umbilicals to the mobile launcher that will provide power to the Space Launch System (SLS) and Orion spacecraft while on the launch pad. Among the major umbilical components the company installed were the crew access arm, which will allow astronauts to climb aboard the Orion spacecraft, and the tail service mast umbilicals, which provide fuel and electrical connection to the rocket.
During peak operations, the company had approximately 120 employees assembling the launcher, bringing NASA one step closer to putting the first woman and next man on the Moon. Bragg Crane & Rigging Co. is looking forward to supporting NASA’s missions to the Moon and beyond in the coming months under a new contract to continue to prepare the Vehicle Assembly Building for the integration of the massive SLS rocket.