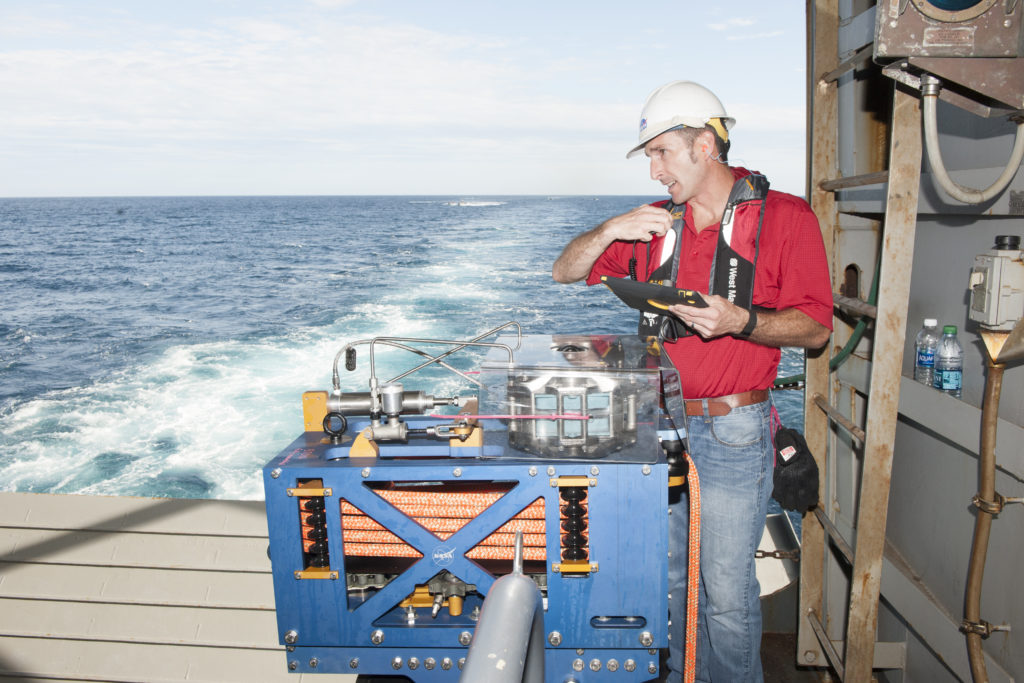
What is a LLAMA? It’s a Line Load Attenuation Mechanism Assembly, designed by Jeremy Parr, a mechanical design engineer in the Engineering Directorate at NASA’s Kennedy Space Center in Florida. He designed the LLAMA to help U.S. Navy line handlers retrieve the Orion crew module after it splashes down in the Pacific Ocean.
Parr is the lead design engineer for Orion Landing and Recovery, which is coordinated and led by the Ground Systems Development and Operations Program. Parr’s design recently earned him second place in the agency’s third Innovation Awards competition.
“The LLAMA concept came to me after watching the sailors fighting to control the Orion test capsule during Underway Recovery Test 1 in open water in February 2014,” Parr said.
The standard Navy line tending practice is to wrap their lines around the ship’s T-bits, or large solid columns with a crossbar that resemble the letter “t,” located near the stern, so that the sailors can control big loads with only a few people. This works for most operations they do since the hardware they handle is usually big and slower moving in the seas. But the crew module is a different beast when floating in the water than anyone on the recovery team expected, Parr said. Orion is easily pushed around by wind and waves.
“I came up with a design that helps the Navy line handlers to safely maintain high tension in the tending lines during recovery of Orion into the well deck of a ship. It also regulates the amount of tension in the lines to ensure equal loading on the vehicle.”
The LLAMAs are mounted on the ship’s T-bits, and the mechanisms provide all tending line control of the crew module once it enters the well deck and until it is secured on the recovery cradle pads.
“I am both excited and honored to be recognized for the LLAMA design,” Parr said. “This has been a team effort for a few years now to get where we are today. We worked through development and testing until we completed our successful test during Underway Recovery Test 5 off the coast of San Diego in the fall of 2016.”
The LLAMA-controlled tending lines are the baseline method for recovery of Orion after Exploration Mission-1 and all future missions.
Parr began working at Kennedy in 2007. Prior to that, he worked for SAIC at Johnson Space Center in Houston for four years.